Coloring your Seals May Deliver Significant Benefits
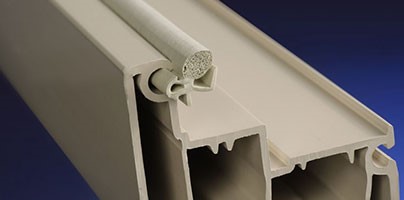
“Any color the customer wants, as long as it’s black”
-Attributed to Henry Ford, on the Model T.
The default seal color has traditionally been black, which many customers utilize. However, an increasing number of customers are discovering the benefits of coloring or partially coloring their seals and related products.
Colored seals offer more than just aesthetic appeal; they can provide various advantages that may surprise you and open up new possibilities.
Design, Branding, Quality Assurance, Installation Ease and More
Most people associate colored seals with enhancing the appearance of devices or equipment, allowing the seal to blend in rather than stand out in its environment. One example of this would be color matching the seal to the eggshell white of a window to appear more seamless.
Branding is another common reason for using colored seals, such as matching a specific corporate logo color.
A less obvious benefit of color is its role in quality assurance, serving as a quick visual indicator. Color can be applied strategically to a part, and installers and quality assurance personnel can identify whether the part is assembled correctly based on the visibility of the color at specific subassembly stages. If it’s not correct, then intervention may be necessary before moving on to the next step of the installation process.
Seals that are similar in size and shape can be colored differently to assist installers in easily selecting the most suitable seal for the installation. Alternatively, if seals are placed adjacent to each other, installers can be instructed to position the seals accordingly based on the color.
Coloring Isn't Always Easy
One reason seal users may overlook the benefits of color is that certain materials, particularly organic ones like EPDM, nitriles, and other sponge materials, are challenging to color, and many seal manufacturers do not offer this option. Even for materials such as thermoplastics and silicones, which are easier to color, additional steps or equipment are still necessary. Some manufacturers may be reluctant to invest in these resources to provide more options for their customers.
At Cooper Standard ISG, we excel in coloring a wide range of materials, backed by decades of experience and a robust profile of proven formulas for various material/color combinations. By compounding and extruding most materials in-house, we maintain hands-on quality control, avoiding the complications of coordinating with multiple parties. Since processing can significantly affect color presentation, we focus on the entire manufacturing process, from raw material to finished product. Additionally, our investment in an in-house photo spectrometer enables us to verify colors by wavelength, ensuring accuracy and consistency across parts.
Some Caveats with Color
While coloring provides numerous benefits, there are certain sealing projects where it may not be advisable, but it's also beneficial to be aware of potential issues on your own.
One of the biggest concerns is that the black coloring in seals typically comes from carbon black, which not only provides a deep black color but also enhances tear strength and abrasion resistance, crucial for certain applications. Removing carbon black for a brighter color can compromise these properties, so it may be beneficial to retain that black coloring in some cases.
Adding color can affect the high-temperature performance of EPDM. Therefore, for applications exposed to temperatures of 150°C/302°F or higher for extended periods, it may be advisable to avoid coloring. Additionally, some materials can dull the vibrancy of colors, so it’s important to manage expectations accordingly.
Coloring can also enhance properties. For example, incorporating red iron oxide into silicone can improve heat performance, leading users to choose this additive even if they don’t require the red color.
Ultimately, while coloring seals can provide numerous advantages, it should be evaluated on a case-by-case basis to ensure optimal functionality and performance. Reach out to the Cooper Standard ISG team regarding your current or upcoming sealing projects, and let’s explore how coloring could benefit you.