In-House Shop For Extrusion Tooling
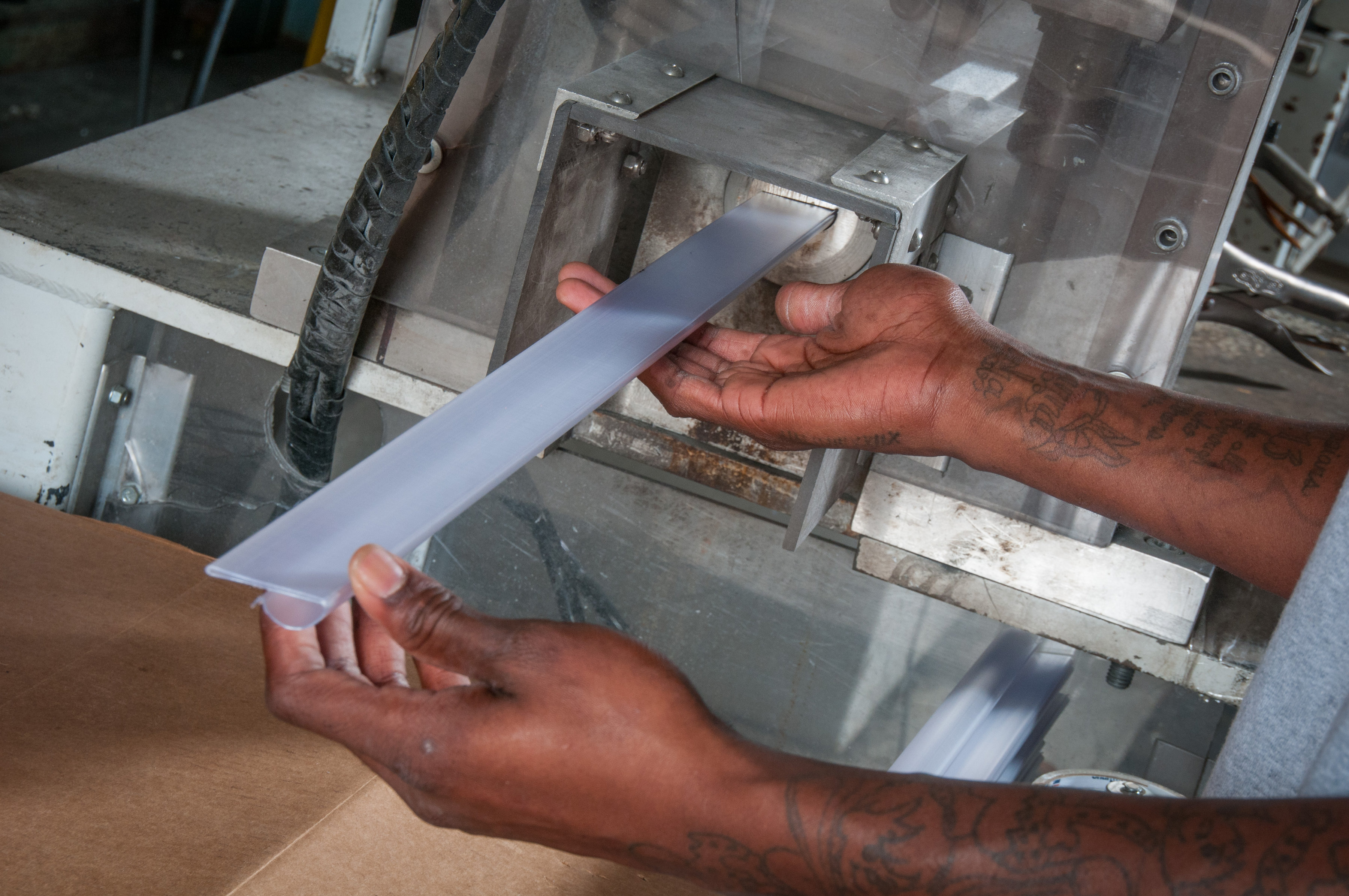
Our Spring Lake, Michigan facility serves as Cooper Standard ISG's thermoplastics sealing center, where many employees, including myself, have been around for decades.
Having invested in our own machine shop for producing extrusion dies in-house, just steps from the production floor, gives us a significant advantage over many thermoplastic seal suppliers who still rely on third-party die cutting services.
A Great Extrusion Die - Key to a Great Product
If you manufacture thermoplastic seals for industries such as commercial trucking, window and door and other industrial applications, you understand that the accuracy of the profile and tolerances of the stainless-steel extrusion die is crucial for successful seal production and high-performing products.
Even the most skilled toolmakers often go through a repetitive process in tool development. You may get it 99+% correct, conduct a test run, and then return to the machine shop for minor adjustments. For larger or more complex dies, multiple iterations are usually necessary. This meticulous attention to detail takes time, but it is essential for achieving long-term effective performance.
Reflecting on the past, I remember when we had to rely on third-party machine shops to produce extrusion dies for our clients back in the ‘90s.
The Old-Fashioned Way
Back in the day, after testing a new extrusion die from our local machine shop, I would typically identify a few areas for improvement. I’d call the machine shop, explain the situation and try to schedule an appointment. When the appointment arrived, which could be days later, I’d remove the die from the extruder, drive over, navigate traffic, find parking and hope my contact wasn’t delayed. Then, I’d explain my needs, plead for machine time and hope to get on the schedule promptly, all while crossing my fingers.
There was also always someone from another company who seemed to always be there when I was. Nice guy, but he was trying to grab up my Wire EDM time. Sometimes they would make us arm wrestle to see if they would cut mine first or his. Just kidding, but they would have to somehow fairly accommodate the conflicting demands of a lot of people.
And, of course, I would likely have to go through this several times for each and every die our customers needed.
So Much Better Now
I have to admit, that machine shop serviced the heck out of us, and all of their customers, which I always appreciated. But still, contrast that with how we make your thermoplastic extrusion dies now. We test the initial die and note any need for improvement. I pull the die, walk 75 steps (yes, I counted) to our in-house machine shop. I talk with one of our four expert Cooper Standard technicians—pros with decades of tooling experience—with direct access to a state-of-the-art CAD/CAM system, three Wire EDMs, two CNC mills and a CNC lathe. And we can collaborate in real-time and take the time needed to ensure that every aspect of the die meets our highest standards.
Some difference.
So, what does that all mean for our thermoplastic seal customers? It means that we can produce a highly precise extrusion die for your tonneau cover seal, glass run channel seal, sidelight seal, or other vital thermoplastic component faster, easier, with tight control and more consistent quality every step of the way. Further, it also allows us to make our own calibration tooling, which compounds these benefits. But that is a story for another day.
At the end of the day, in-house tooling has led to significantly faster development times and improved product quality for our customers.
And for me, I don’t have to keep driving cross town.