Welcome to Spring Lake!
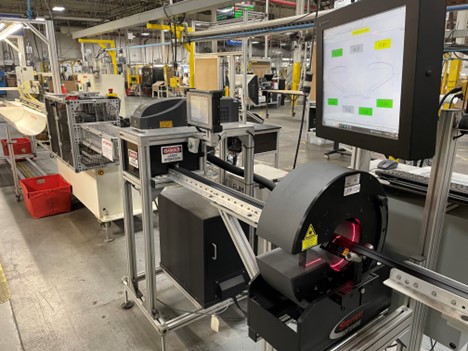
As the plant manager at Cooper Standard’s Spring Lake facility, I take great pride in our achievements. As the primary thermoplastic extrusion plant for Cooper Standard ISG, we diligently serve our customers daily, producing over 425 different thermoplastic sealing components from 78 different materials, utilizing over 200 unique dies for 76 diverse customers across industries like commercial trucking, windows & doors and enclosures. “Safety First” is one of our core values and something we take very seriously. We prioritize safe operations and environmental respect while fostering a team-oriented, family-like culture.
I credit our success to our dedicated team of about 80 members. I prioritize getting to know each one personally, as one of my biggest concerns is encountering someone in the plant without knowing who they are and their role in the company. To prevent this, I conduct the onboarding training myself, ensuring that I’m on a first-name basis with everyone. I want all members of my team to feel comfortable approaching me with any concerns, and my door is always open to everyone.
A Great Extrusion Die - Key to a Great Product
If you manufacture thermoplastic seals for industries such as commercial trucking, window and door and other industrial applications, you understand that the accuracy of the profile and tolerances of the stainless-steel extrusion die is crucial for successful seal production and high-performing products.
Even the most skilled toolmakers often go through a repetitive process in tool development. You may get it 99+% correct, conduct a test run, and then return to the machine shop for minor adjustments. For larger or more complex dies, multiple iterations are usually necessary. This meticulous attention to detail takes time, but it is essential for achieving long-term effective performance.
Reflecting on the past, I remember when we had to rely on third-party machine shops to produce extrusion dies for our clients back in the ‘90s.
A High-Mix Operation
We certainly stay busy, operating continuously from Monday-Friday night, 24 hours a day. However, there is a lot that sets us apart from many other extrusions operations.
While many facilities focus on a few customers and high volumes of a single part, at Spring Lake we work with dozens of customers, producing hundreds of components for each of them. Few facilities offer the variety of plastics that we do, constantly developing new profiles with different thermoplastic materials and durometers, ranging from flexible to rigid and all colors
Adding Value in Many Ways
Our operation stands out in several ways, particularly when compared to other thermoplastic manufacturers. For example, we excel in performing secondary operations after the initial extrusion, preparing parts for installation at our customers’ facilities. We cut, punch, trim, and add adhesive strips, rivets or brackets – essentially whatever our customers need to save time and money while streamlining their assembly processes. We’ve also made significant investments in robotics for certain cutting and trimming, allowing us to handle large complex multi-durometer profiles on a consistent, repeatable basis.
Additionally, we have a world-class machine shop on-site that allows us to produce our own dies in-house. This capability ensures tight quality control and accelerates the development process.
Recycling is a High Priority
Nearly all of our scrap thermoplastic material is recycled or reused in some way, either ground down and mixed with virgin material in some grades or sold to a specialty company for energy and other purposes. Our goal is minimizing landfill contributions. In fact, one of my team’s proudest accomplishments is the relative emptiness of our dumpsters.
Family Culture
At Spring Lake, we work as a cohesive team with a shared mission to produce high-quality parts safely and sustainably. To further enhance our family culture, we host numerous events for employees such as taco bars, cookouts, bowling parties and even a Thanksgiving Dinner. We also engage in community outreach, participating in events like food drives, blood drives and the Adopt-A-Highway program, where we help clean up the highway section closest to the plant.
We would love to extend an invitation to our valued customers to visit our Spring Lake plant and witness our various processes in action.