Value Added Services For Cost Savings Down The Line
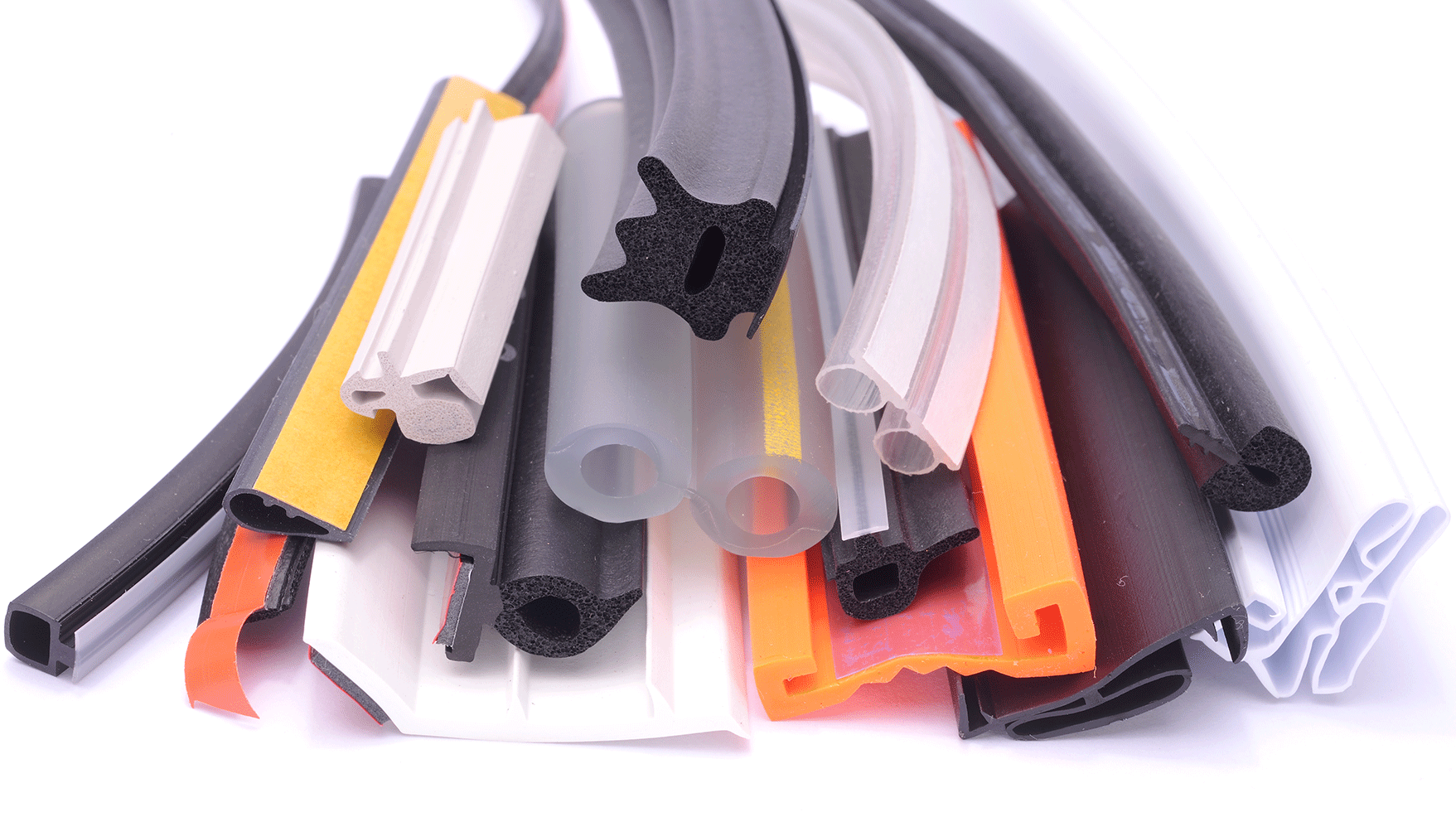
The majority of our partnerships at Cooper Standard ISG, whether they are thermoplastic, rubber, silicone, standard component, or custom engineered, go farther than simply extruding and delivering high quality products. They often include value-added features and delivering cost savings down the line.
Long ago, we realized we could offer a great deal of value in further preparing the seal for final installation. If we know in advance how the customer will be installing the seal, there is likely a lot we can do to optimize the seal for a smoother installation process. Utilizing our value-added services helps our customers not only eliminate the need to hire a third-party installation service, but also reduce additional labor costs and delivery timing.
Precision Machining, Punching Holes, Robotic Cutting and more
We consider every production partnership a potentially wholistic one—after all, if we can help build and deliver a more “turnkey” part, why wouldn’t we do it?
A very common scenario we encounter is a customer having us notch, punch, or drill portions of the extrusion to help create a more seamless assembly. With our expertise in cutting, notching, drilling and more, we can fabricate your extrusion to your exact length and save you time and money down the line.
In addition, we have invested in robotic cutting cells, offering a high-speed routing and ultrasonic knife operation, which can help with many types of low volume cutting, drilling and punching operations. For example, when a component is dual durometer, extruded with two or more different materials, the robot can cut very efficiently. The router machines cut hard materials while the ultrasonic knife cuts the soft materials. As a result, we are left with a precisely fabricated profile extrusion that can stand up to address many demanding challenges.
Adhesive Strips, Pins, Printing, Coatings and more
Adhesive strips are another area where we frequently add value. We identify a compatible adhesive that will provide long lasting performance, adding a promoter as needed to ensure a clean application, and provide it directly on the seal with a peel off strip. At the customers facility, the installer will peel off and press the extrusion to the housing, without having to deal with hot pots of messy adhesive. It can make a big difference.
Slip-coats reduce the coefficient of friction, and some installation processes can benefit by adding a slip coat extruded direction to the part during the extrusion process. This is common across all our materials, including TPVs, a thermoplastic with a very desirable mix of properties which naturally has a bit of a tacky surface. Adding the slip-coat provides customers with a higher performing product when reduced friction is desired.
We also perform a good deal of inline inkjet printing or laser etching, most often for product traceability scenarios such as date of manufacture, or customer part or lot number, but also marketing cues like company or brand name or logo. Inkjet—which is black ink—is a go-to for lighter colored parts, while laser etching can be more versatile and give a higher degree of visibility, if that is desired.
As you can see, there are many possibilities. We just need to put our heads together and see where our capabilities can work to lower your costs and speed your production cycle even more. We can perform add-ons in-line during the extrusion process, saving you money in both manual labor costs and any additional assembly costs. There may be a need for a one-time tooling package, which then works for you long-term.
Interested? Let’s talk. We can give you more than just a great extrusion. We provide high-quality engineered seals for dozens of companies across a wide range of industries.